High Design Freedom: Traditional mold manufacturing is limited by the process. For molds with complex shapes and structures, design and manufacturing are difficult and costly. 3D printing technology can achieve shapes that cannot be manufactured by traditional methods, and it can easily fabricate molds with complex internal structures and conformal cooling channels, optimizing mold performance, improving production efficiency and reducing overall costs.
Reduced Design Change Costs: During product development, if mold design changes are needed, traditional mold manufacturing may require remaking the mold, resulting in huge waste of upfront costs. 3D printing can quickly modify and reprint according to the new design model, reducing the cost increase caused by design changes.
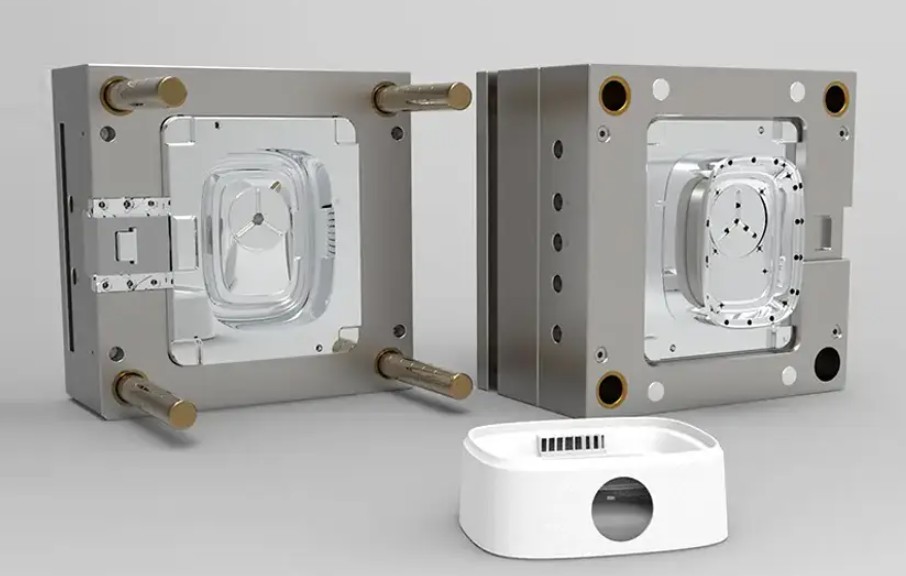
Advantages in Small Batch Customization: For small batch and customized mold requirements, the cost allocation of traditional manufacturing molds is high. 3D printing can produce on demand without having to invest a large amount of mold development costs for small batch orders, and it has obvious cost advantages in small batch customized mold production. For example, after toivalanmetalli adopted 3D printed molds, it achieved small batch production, and the cost per piece was significantly reduced to 300 to 400 euros.
In conclusion, 3D printing technology indeed plays a crucial role in reducing mold costs.