Gas - mold relationship in injection molding
2025-02-19 17:29:42
Gas - mold relationship
The generation of gas during injection molding is intricately linked to the mold across multiple aspects, mainly covering mold design, manufacturing & processing, and usage & maintenance.
Gate: Improper gate location or size, like not at the thick - walled part or being too small, hinders air expulsion and extends filling time, risking gas entrapment. Asymmetric multi - gate setups create complex flow, making gas escape tough.
Runner: Long, narrow runners increase melt resistance, delaying gas discharge. Gas - storage dead corners, such as in odd bends, trap gas.
Ventilation: Insufficient vent holes, wrong positions, or under - utilized auxiliary vents (e.g., from inserts) cause gas - related issues like short shots and burns, especially in high - speed molding.
Cooling: Poor cooling design leads to uneven shrinkage, forming internal voids that can hold gas.
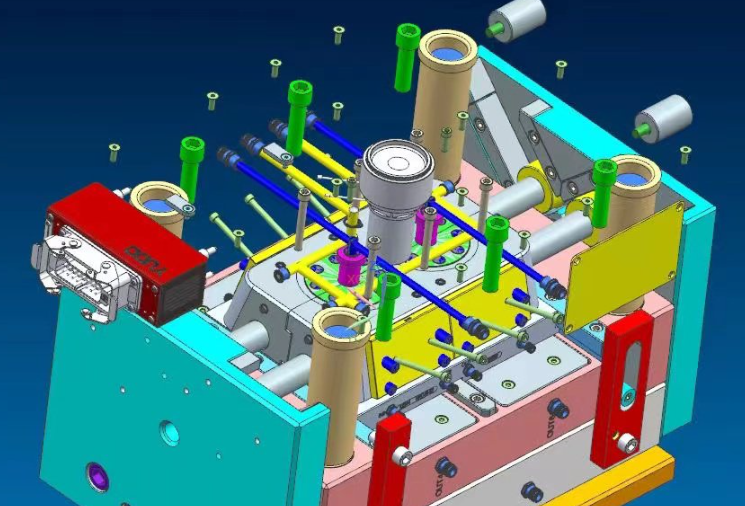
Surface Quality: Rough surfaces with burrs and grooves cause friction - induced overheating and gas accumulation due to melt flow resistance.
Assembly: Poor mold closing or incorrect part - to - part clearances can let air in or block designed vents, affecting gas removal.
Cleaning: Unclean molds with oil, dust, and release - agent residues decompose under heat and pressure, generating gas that degrades product quality.
Wear: Wear on molds, especially in vents and moving parts like ejector pins, narrows or blocks vents, impeding gas escape.
In summary, addressing these mold - related factors throughout its lifecycle is key to minimizing gas issues and improving injection - molded product quality.
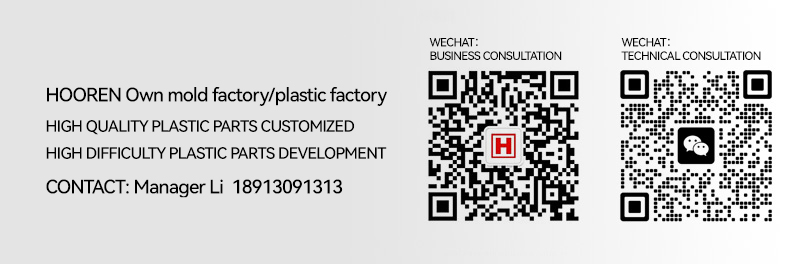