In injection molding, the process has two main stages. In the first, 90% - 99.9% of plastic fills the mold. In the second, the product is compacted, which is vital for surface and dimension quality. This second stage typically uses pressure and time. Scientific molding expands this to four key elements:
The transition method from the first to the second stage.
Processing with the gate sealed or unsealed.
Holding pressure time.
Maintaining proper cavity pressure.
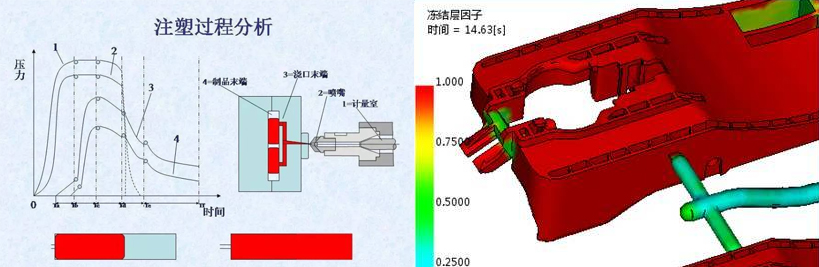
The transition from the first to the second stage is crucial for high - quality production. It should be quick, with the pressure rapidly shifting to the second - stage requirement. Different machines handle this transition differently:
Some have a viscosity - controlled transition function.
Others have a transition viscosity setting that only slows the plunger speed.
Some lack a transition viscosity setting.
And some malfunction during transition, showing viscosity issues.
A fast and consistent transition (under 0.1 seconds) is ideal. Pressure drops, sharp peaks, oscillations, or slow pressure changes during transition are bad. The pressure - time graph helps assess machine response.
Not all products can be processed with a sealed gate. A gate - sealing test is needed. Sometimes products with a sealed gate are better, and sometimes an unsealed one is. Observation alone won't tell; testing is required.
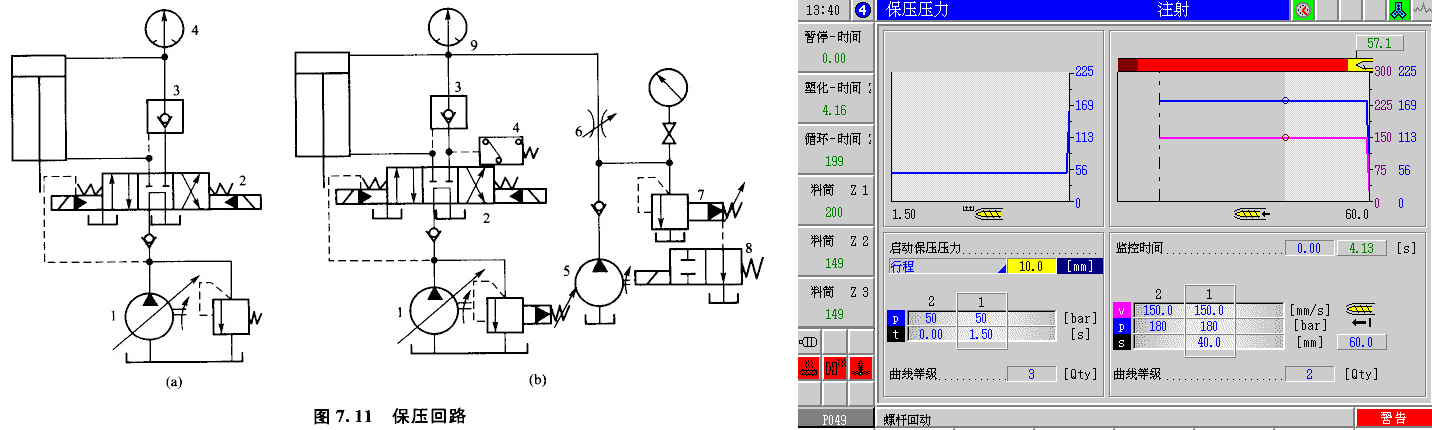
Knowing if the gate should be sealed helps set the second - stage time. If a sealed gate is needed, increase the second - stage time. This may not extend the cycle as cooling or mold - closing time can be reduced. If an unsealed gate is better, start cooling it for half the required time. Consistent cycle time is important when the gate is unsealed.
Finding the right holding pressure is key for product compaction. It should be in the middle of the range for a good Cpk. First, check the first - stage stability. Then, start from a low holding pressure (e.g., 1000 - 2000 psi for plastics), increase it in small steps, and check product quality. Keep increasing until issues like flash occur. Then, reduce to a workable maximum. Make three sets of products: at the start, at the maximum, and at the mid - point of the pressure range. Quality - control data will show if products are too large, too small, or a mix. Based on this, adjust the second - stage pressure to the center of the acceptable range.
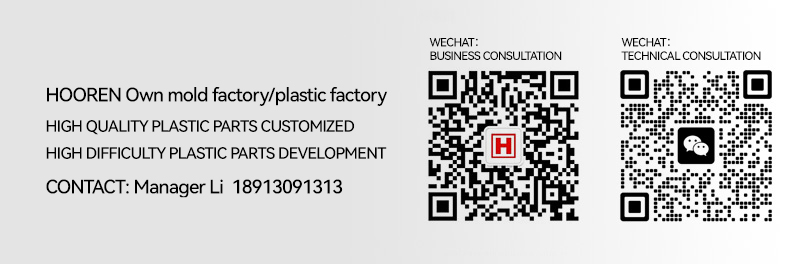